Comprehensive Guide: What is Porosity in Welding and Just How to Prevent It
Comprehensive Guide: What is Porosity in Welding and Just How to Prevent It
Blog Article
Comprehending Porosity in Welding: Exploring Causes, Impacts, and Prevention Methods
Porosity in welding is a relentless obstacle that can considerably influence the high quality and honesty of welds. As professionals in the welding sector are well aware, comprehending the causes, results, and prevention strategies associated with porosity is vital for accomplishing robust and reputable welds. By delving into the source of porosity, examining its destructive effects on weld top quality, and discovering reliable avoidance methods, welders can boost their knowledge and abilities to create high-quality welds continually. The complex interplay of aspects contributing to porosity requires a comprehensive understanding and an aggressive method to make certain successful welding outcomes.
Common Root Causes Of Porosity
Contamination, in the kind of dust, grease, or corrosion on the welding surface, produces gas pockets when warmed, leading to porosity in the weld. Improper protecting occurs when the securing gas, commonly made use of in procedures like MIG and TIG welding, is unable to completely shield the liquified weld pool from responding with the surrounding air, resulting in gas entrapment and subsequent porosity. In addition, inadequate gas insurance coverage, typically due to wrong flow rates or nozzle positioning, can leave parts of the weld unsafe, permitting porosity to form.
Results on Weld High Quality
The visibility of porosity in a weld can significantly endanger the overall high quality and honesty of the bonded joint. Porosity within a weld produces voids or cavities that compromise the structure, making it much more at risk to breaking, deterioration, and mechanical failing.
Additionally, porosity can hinder the effectiveness of non-destructive screening (NDT) strategies, making it challenging to identify various other issues or discontinuities within the weld. This can lead to substantial safety and security problems, particularly in critical applications where the architectural stability of the welded parts is critical.

Avoidance Techniques Overview
Given the damaging influence of porosity on weld high quality, effective avoidance techniques are important to keeping the architectural honesty of welded joints. One of the key avoidance techniques is thorough cleaning of the base materials prior to welding. Impurities such as oil, oil, rust, and dampness can contribute to porosity, so ensuring a clean job surface is important. Proper storage space of welding consumables in completely dry problems is additionally crucial to avoid moisture absorption, which can bring about gas entrapment during welding. Additionally, picking the suitable welding specifications, such as voltage, current, and travel rate, can aid decrease the risk of porosity formation. Making sure adequate protecting gas flow click for more info and protection is one more essential prevention method, as insufficient gas protection can result in climatic contamination and porosity. Lastly, correct welder training and accreditation are essential for carrying out safety nets efficiently and consistently. By including these avoidance techniques into welding methods, the incident of porosity can be considerably reduced, leading to more powerful and much more reliable bonded joints.
Relevance of Correct Shielding
Proper shielding in welding plays a vital role in stopping atmospheric contamination and making sure the stability of bonded joints. Protecting gases, such as argon, helium, or a mix of both, are commonly utilized to shield the weld swimming pool from reacting with elements airborne like oxygen and nitrogen. When these responsive elements come right into contact with the warm weld pool, they can create porosity, bring about weak welds with minimized mechanical residential or commercial properties.
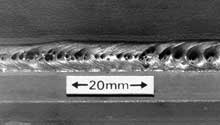
Poor protecting can result in different issues like porosity, spatter, and oxidation, compromising the structural stability of the bonded joint. Sticking to correct securing practices is essential find to generate premium welds with very little issues and make certain the long life and reliability of the bonded components.
Surveillance and Control Techniques
How can welders efficiently keep an eye on and regulate the welding procedure to ensure optimal results and stop problems like porosity? By continually checking these variables, welders can identify discrepancies from the perfect conditions and make instant changes to prevent porosity formation.

Furthermore, executing appropriate training programs for welders is important for checking and managing the welding procedure successfully. What is Porosity. Informing welders on the value of preserving regular parameters, such as correct gas protecting and take a trip rate, can assist prevent porosity problems. Routine assessments and qualifications can also guarantee that welders excel in monitoring and regulating welding procedures
Furthermore, using automated welding systems can improve monitoring and control abilities. These systems can precisely manage welding specifications, reducing the chance of human mistake and making certain constant weld high quality. By incorporating innovative monitoring modern technologies, training programs, and this article automated systems, welders can efficiently keep an eye on and regulate the welding procedure to reduce porosity issues and achieve top quality welds.
Conclusion
Report this page